3 MOT Tesla Coil
The big Tesla Coil
I developed this project when I was 15 years old. Prior to this, I had built small Tesla coils using recycled parts from electric flyswatters and old TV components, but I wanted to create something capable of generating electric arcs of at least 1 meter in length.
Given my age, I didn’t have the budget to purchase new components, so for several weeks, I focused on collecting broken microwave ovens from the street and salvaging copper coils from old televisions. Once I had gathered enough parts, I was able to assemble the project, achieving incredible results, though with a few transformers burned in the process.
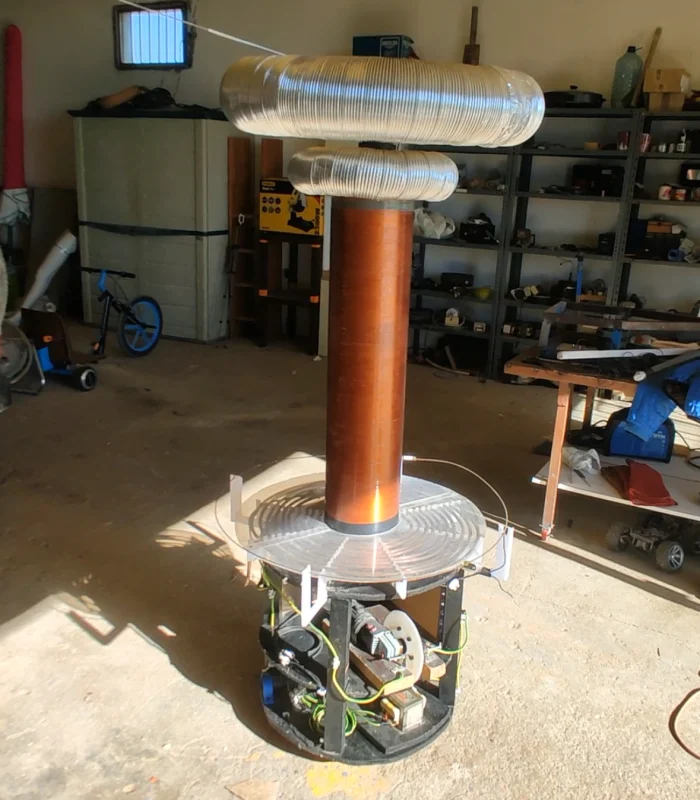
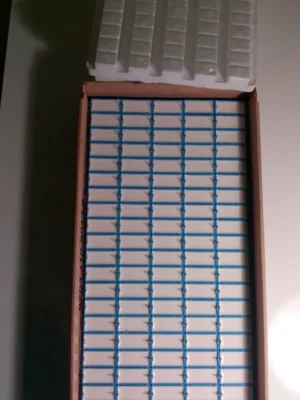
Specifications
– Spark Gap Tesla Coil
– Power supply: 3 microwave transformers in series, 6300V 0.5A
– Power: 3 kVA
– Spark gap: Angle grinder, 11,000 rpm, 6 rods
– Resonant frequency: 85 kHz
– MMC: 133 capacitors, 19 kV, 125 nF
– Primary coil: 7 tuned turns
– Secondary coil: 1000 turns
Primary and secondary design
The primary resonant circuit is designed for a frequency of approximately 85 kHz. The capacitor is made using 133 capacitors of 330 nF and 1000 V, arranged in series and parallel to create an MMC capable of withstanding the overvoltages generated in the capacitor during resonance. In this case, the voltage rating considered is three times the nominal value, 19 kV and 125 nF.
On the other hand, the primary circuit has been modified several times. Eventually, a flat coil design was chosen because the magnetic coupling between the primary and secondary was too strong, causing discharges between the windings of both coils. A sheet of acrylic was also used to prevent this phenomenon. Finally, the tap was adjusted to 7 turns.
The design of the secondary coil was also influenced by discharges between the windings due to the extremely high voltages. This coil was designed with 1000 turns, but the main issue, due to using recycled material, was that some areas had insulation problems. To solve this, the coil was coated with four layers of insulating varnish for wood.
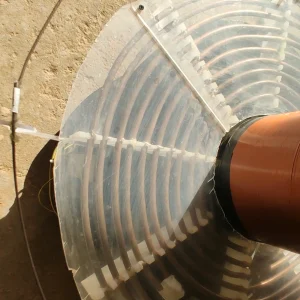
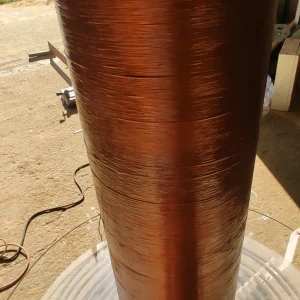
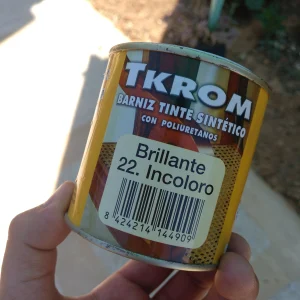
Resonant circuits and spark gap
When using classic Tesla coils, the charging and discharging of the capacitor and coil are not continuous and need to be regulated in some way. This is where the spark gap comes into play. When the capacitor is charged to a sufficient voltage, it discharges, forming an LC circuit with the primary coil, resonating at 85 kHz. Once the resonant circuit loses energy due to resistive effects and transfer to the secondary coil, the spark gap de-ionizes, stops conducting, and begins a new capacitor charging cycle.
The main issue with this project was that, due to the extremely high currents in the primary coil, the spark gap rods would melt within seconds. The solution was to use an angle grinder with electronically controlled speed, ranging from 0 to 11,000 rpm, and equipped with 6 electrodes. This significantly reduces wear and helps cool the electrodes as they rotate.
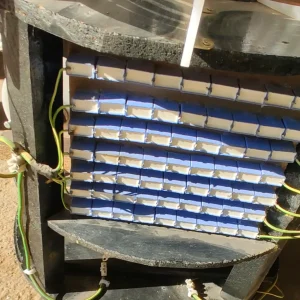
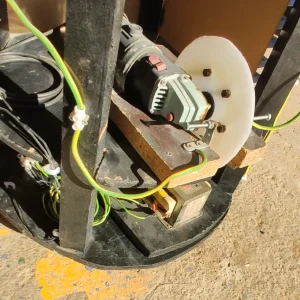
Power supply and control
As mentioned, the power supply is completely recycled and was built using used microwave oven transformers. Each transformer generates a voltage of 2100 V with 1000 VA, resulting in a current of 0.5 A. These current values can be lethal to a person in seconds. To achieve sufficient voltages for the circuit to function, it was decided to use 3 MOTs with the primaries connected in parallel and the secondaries in series, maintaining the winding sequence and generating 6400 V.
For controlling the entire system, a simple control box was built. It directly powers the transformer circuit through a thermal magnetic switch using a single-phase network. As for the spark gap, speed regulation is allowed through a simple cutting circuit with an SCR and a DIAC.
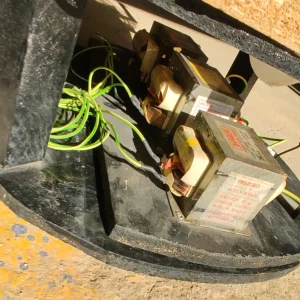
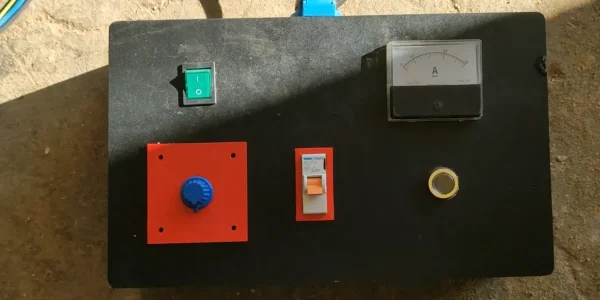
Test and Results
After many tests, the Tesla coil was successfully tuned to achieve optimal performance.
The first discharges were only 30 cm long, but by adjusting the resonant frequency through simple tests, such as tweaking the primary winding and observing whether the electric arc increased, discharges of up to 1.8 meters in length were achieved — not bad at all.
Later, for some electrical tests, a Faraday cage was built to allow for close observation of the electrical discharges without risk of harm.
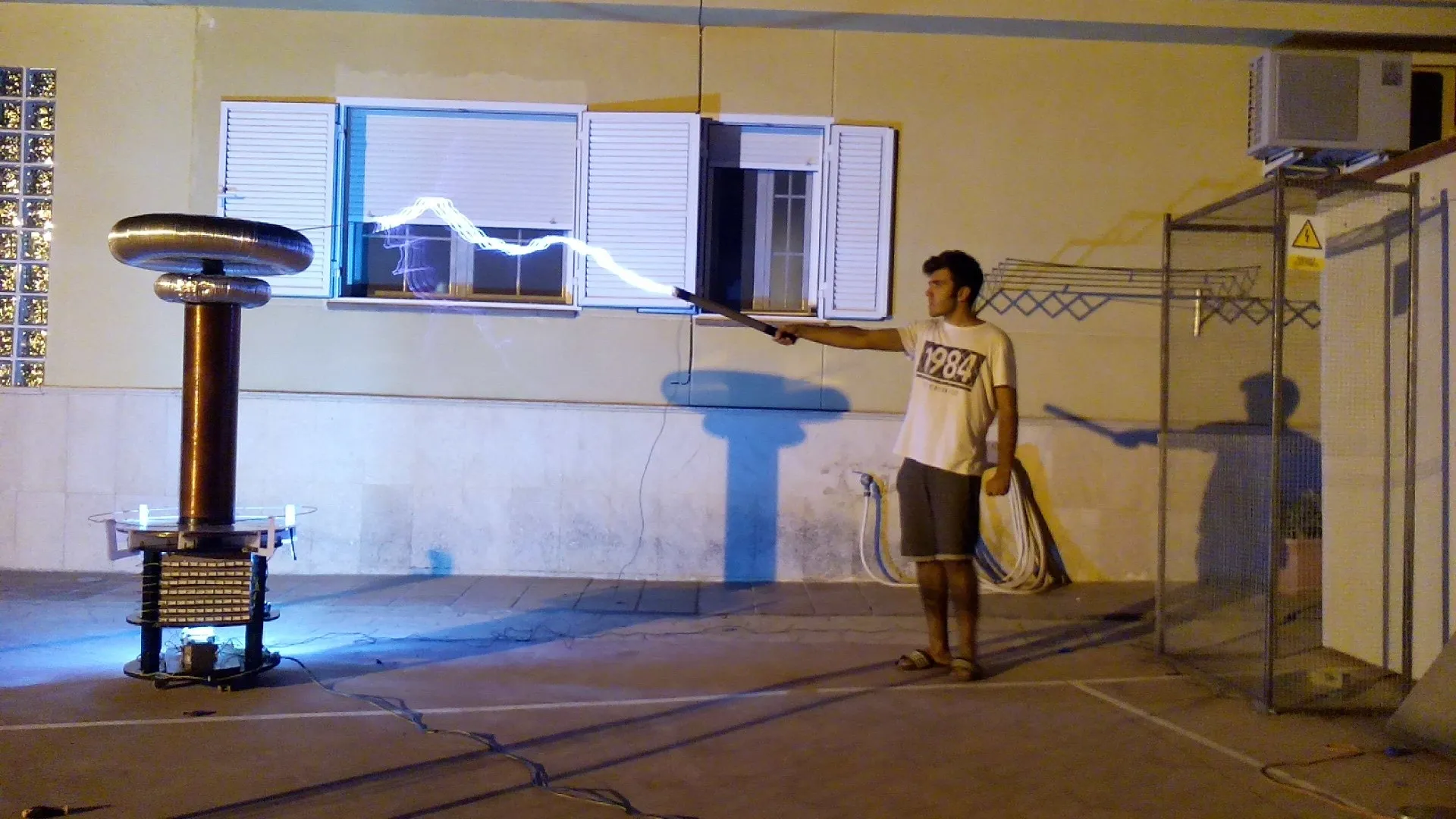
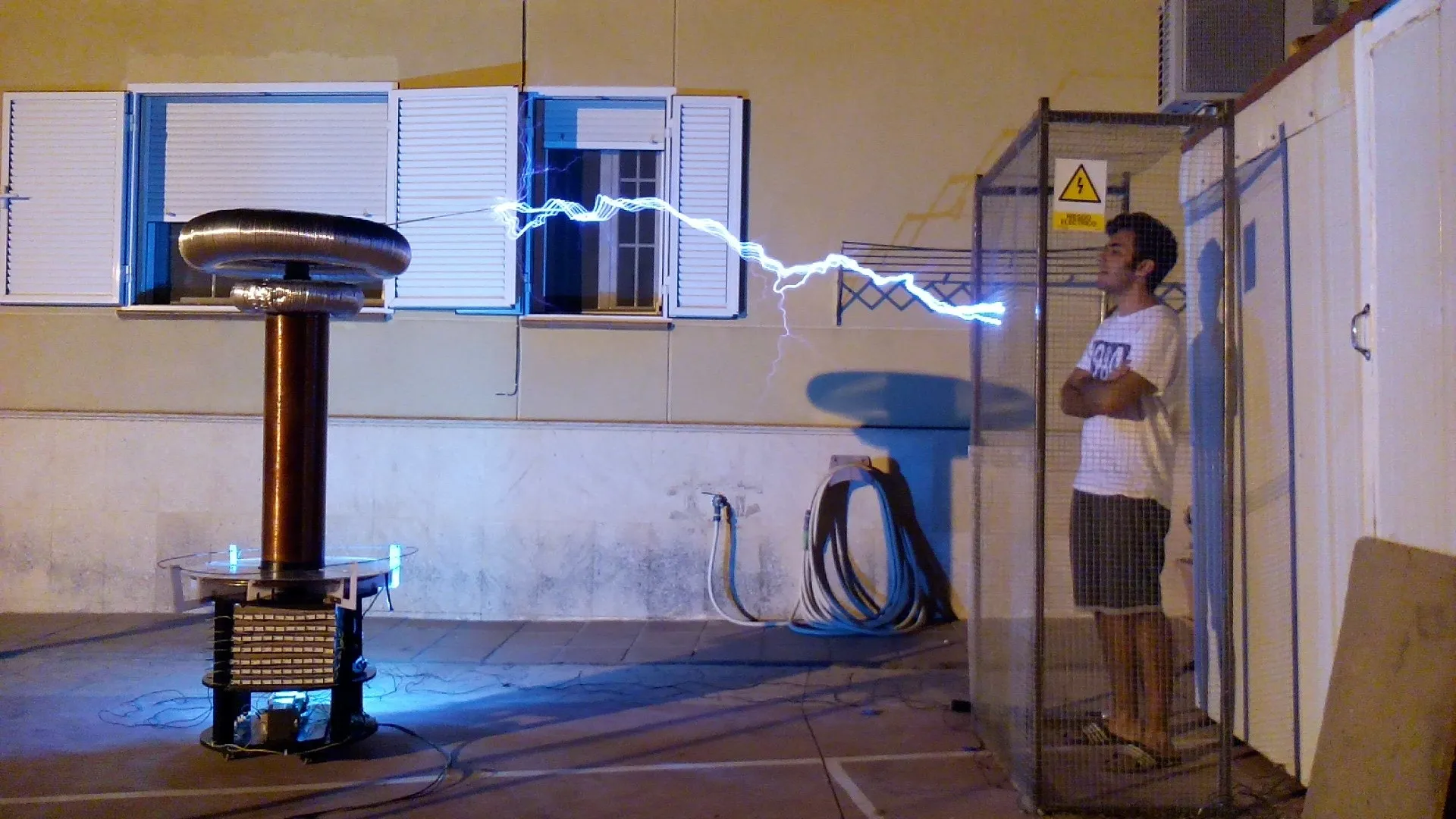