Guided Minigun
Launching rockets
This project began in 2024 when I saw a helicopter with a machine gun that automatically aimed wherever the pilot’s helmet was pointing. From a technical standpoint, it didn’t seem overly complex, so we decided to start designing our own version. After just a couple of months of development and prototyping, the result was this incredible engineering project.
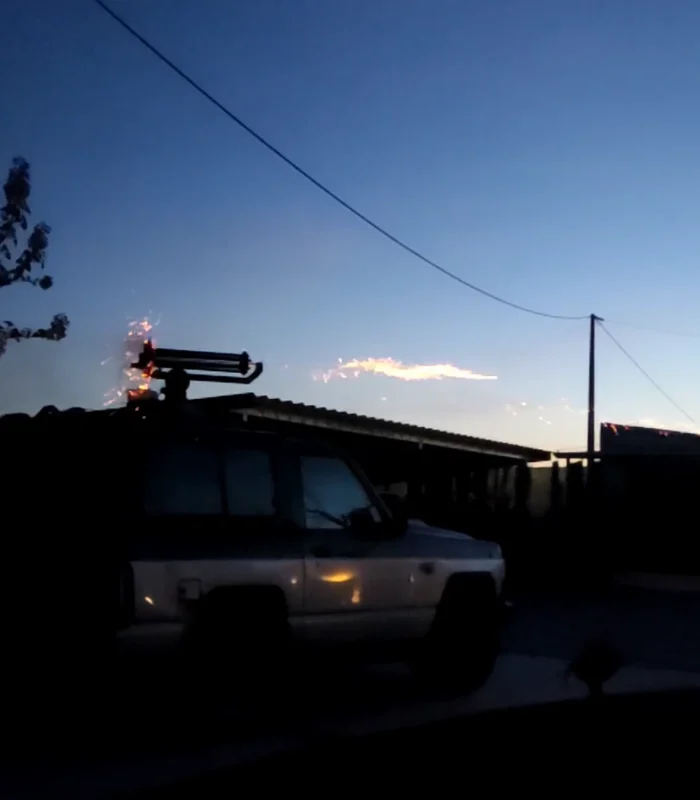
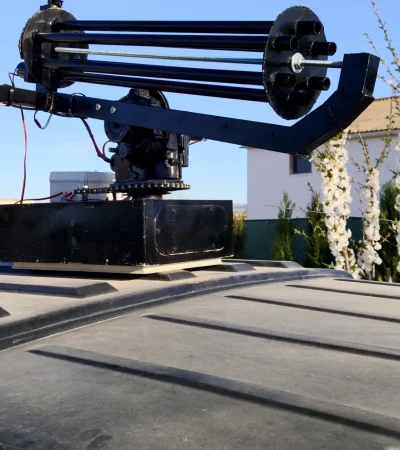
Specifications
– Two degrees of freedom motion
– Position control using a 6-axis IMU (accelerometer and gyroscope) and magnetometer
– FPV helmet vision with direct orientation tracking
– 15-gram rocket launchers
Building the gatling machine
The physical design of the system is not particularly complex—the real challenge lies in the electronics and control systems. In this case, the build was designed with two degrees of freedom: vertical (up and down) and horizontal (left and right) movement. Since the system is intended to be mounted on a vehicle, additional degrees of freedom were not necessary.
Vertical motion is achieved using a 1:10 gear reducer made from the gearbox of a 49cc motorcycle. This reducer is coupled to a 12V, 55W motor that includes its own gear reduction system, outputting 150 RPM. As a result, the final joint achieves around 15 RPM, which is sufficient for targeting purposes. The horizontal axis uses a 1:6 bicycle gear connected to a windshield wiper motor running at 60 RPM. This configuration delivers a final rotation speed of about 10 RPM, allowing for smooth and accurate lateral movement. The firing mechanism operates with a motor that rotates a six-barrel drum, each barrel measuring 16 mm in diameter—enough to load the projectiles effectively. The entire assembly is mounted on a custom metal platform.
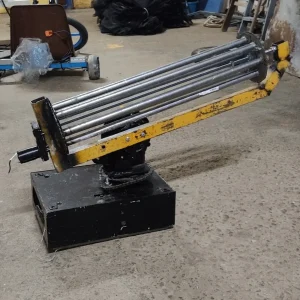
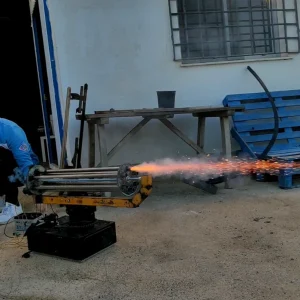
Control and aim
The aiming and control system is the most complex part of the project. It relies on a transmitter located in the helmet, which sends real-time orientation data to a receiver mounted on the turret. Both the transmitter and receiver are powered by Arduino microcontrollers—an Arduino Nano in the helmet and an Arduino Mega in the cannon system.
Communication between the two units is established using NRF24L01 radio frequency modules via the SPI protocol. Both the helmet and the turret are equipped with identical sensors: a magnetometer, accelerometer, and gyroscope. The orientation data from the helmet is transmitted to the receiver, where it is compared to the turret’s current position in order to align the system precisely with the operator’s line of sight. To enhance accuracy, a complementary filter with tilt compensation is implemented, minimizing axis coupling errors and improving the overall responsiveness and stability of the targeting system.
The orientation data received by the turret is processed by comparing the magnitudes from both the helmet and the onboard sensors. Several PID controllers are implemented to calculate the necessary corrections, and the resulting output is sent as PWM signals to the motor drivers. The system uses BTS7960 motor drivers, which are capable of handling currents up to 40A, providing robust and reliable control for the high-torque motors used in the platform.
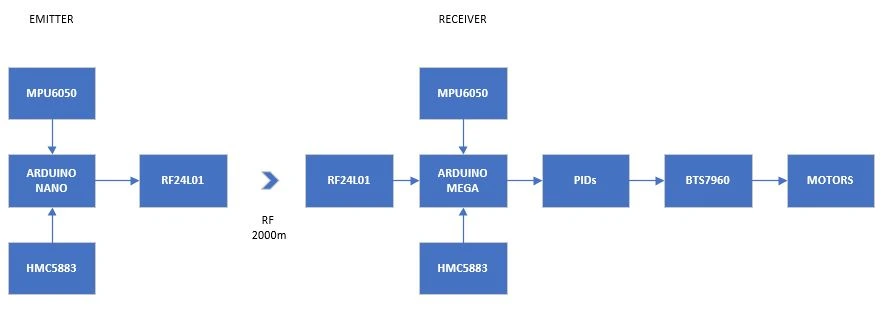
FPV system
The FPV system provides the operator with the same field of view through the helmet as seen from the turret-mounted machine gun, making it significantly easier to aim at targets. This setup is built using an FPV camera and a 720p image display, connected over multiple channels operating at a 2.4GHz frequency.
The projectiles used are pre-manufactured rockets weighing approximately 20 grams. To ensure precise firing timing, an electric ignitor is triggered via a limit switch. The ignitor activates a filament, which in turn ignites the rocket. The entire system is powered by a 12V battery, providing consistent and portable energy supply for both targeting and launching components.

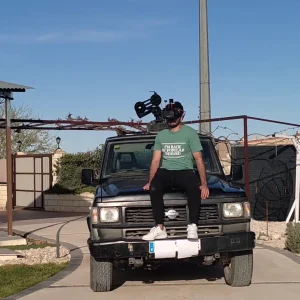
Results in a 4x4 car
The entire system was mounted on the roof of a 4×4 vehicle, and the results were nothing short of impressive. While driving, maneuvering the turret can be somewhat challenging due to the lack of peripheral vision, so the ideal setup would involve two operators—one for driving and another for aiming and firing.
The system’s response time is extremely fast, allowing the cannon to track targets effortlessly by simply moving the operator’s head. This makes it highly effective for mobile platforms that need to remain alert and responsive in dynamic environments.
Multiple test firings were conducted using 20-gram rockets, both during the day and at night, with excellent results. Even while driving and aiming simultaneously, the system performed well. Thanks to the real-time FPV feed—with a latency of only 20ms—the operator can also navigate using the helmet view, making the platform viable even in motion.
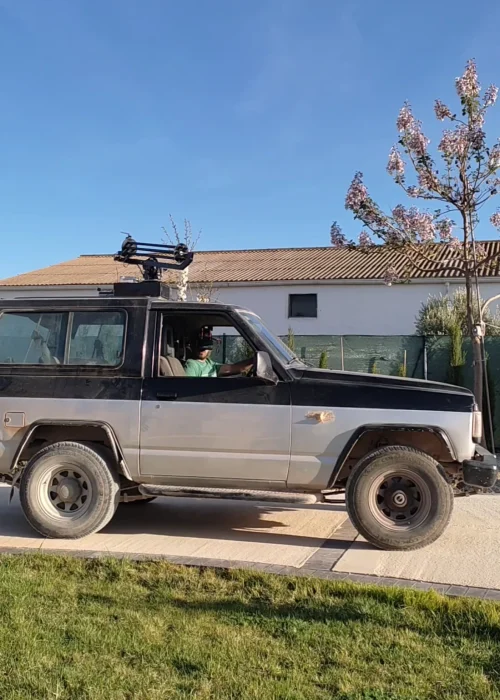